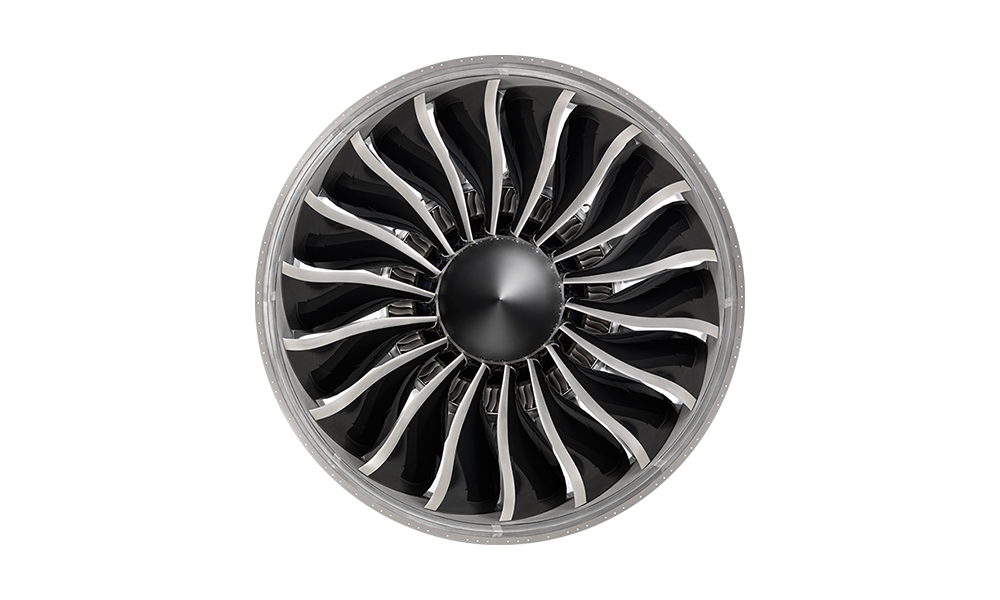
Advanced blade aerodynamic design for next-generation jet engines
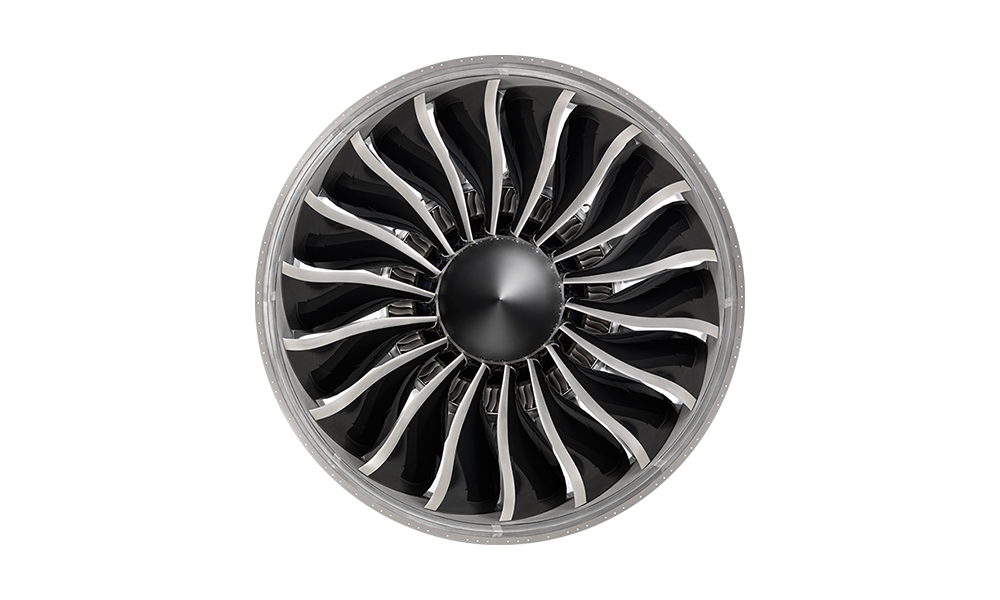
Project name: Advanced blade aerodynamic design for next-generation jet engines
Research group: Aerospace Science and Technology
Objective
Description
To meet the ever demanding need of increased fuel efficiency and reduced emissions, advanced numerical tools are developed to assist the designers. In partnership with a leading engine manufacturer, novel numerical models extend high-fidelity computational fluid dynamic softwares to estimate the sensitivity of performance metrics to design parameters using control theory.
The computational domain consists of multiple blade passages, one for each row, using periodic boundary conditions to model the complete blade row and mixing plane interfaces to model the interaction between adjacent rows.

The process involves solving both the flow governing equations, namely the Reynolds-averaged Navier-Stokes, and the corresponding adjoint equations for each performance metric of interest, such as efficiency, pressure ratio or mass flow.


The resulting adjoint solutions are then used to evaluate the derivatives of the performance metrics with respect to the selected design variables. These design variables can be the shape of the blades and hub/casing, but can also be the inlet or exit flow conditions.


The adjoint method computational cost is approximately the same as that of the flow solution and, In contrast to other sensitivity analysis methods, it is nearly independent of the number of design variables.
References
- S. S. Rodrigues and A. C. Marta, Adjoint formulation of a steady multistage turbomachinery interface using automatic differentiation, Computer and Fluids, Vol.-, Issue -, pp.–, September 2018 (in press). doi: 10.1016/j.compfluid.2018.09.015.
- A. C. Marta and S. Shankaran, Assessing turbomachinery performance sensitivity to boundary conditions using control theory, AIAA Journal of Propulsion and Power, Vol.30, Issue 5, pp.1281–1294, September 2014. doi: 10.2514/1.B35087.
Contact Person
André C. Marta